You might equate automation with increased throughput and reduced hands-on involvement, and you’d be right. What you might not know, however, is that the way that you approach automation is just as important as the robot itself.
What does that mean? In a nutshell, it means that by looking at laboratory operations from multiple angles and applying small, easy-to-implement changes, forensic DNA labs can develop automated workflows that maximize efficiencies and make notable impacts not only to sample backlog and turnaround time reductions, but quality metrics as well. Here, are some insights to ease your successful transition into your very own automated ecosystem.
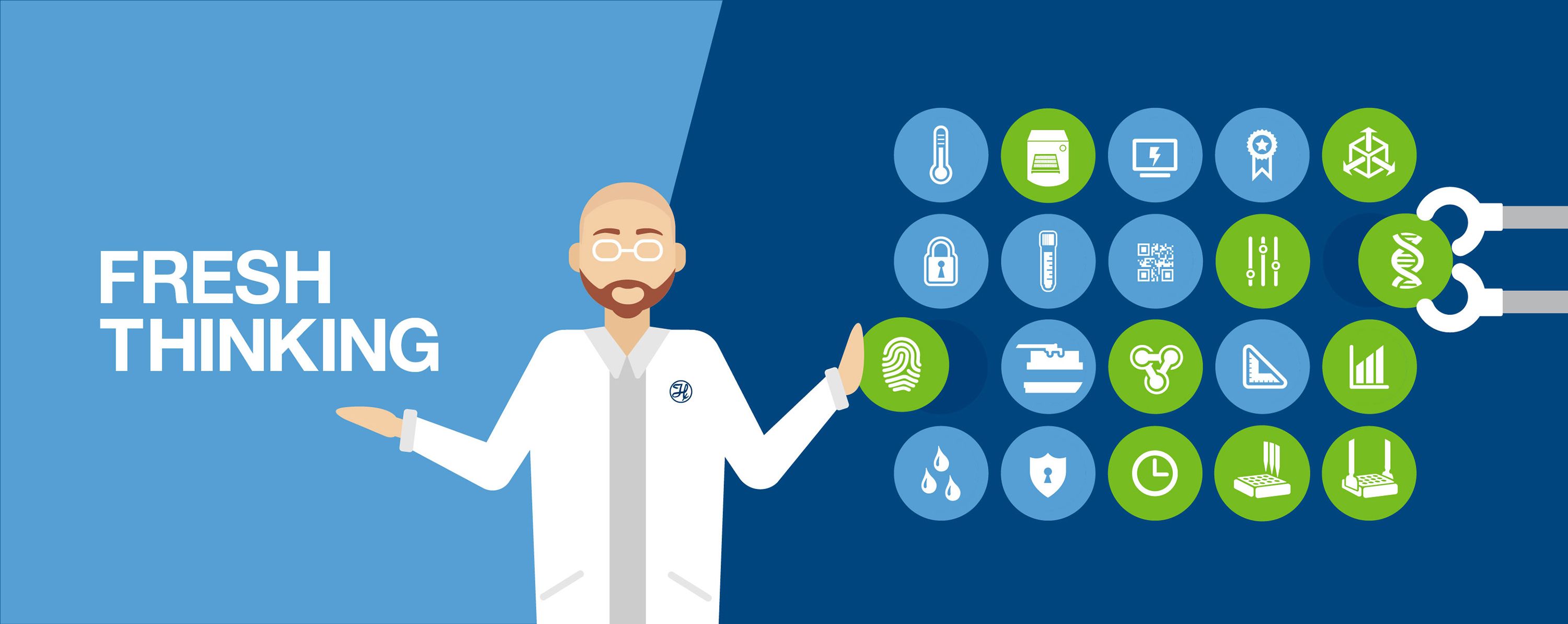
Bye-Bye Plug & Play, Modular is the Modern Way
Is transitioning a task from manual to automated as simple as your word processing software’s find/replace function? Of course not. Although, this does happen when providers restrict their robotic solutions to work exclusively with their assay chemistries.
The “plug & play” or “modular” approach to automating individual workflow steps (e.g. nucleotide extraction) seems straightforward, relatively inexpensive, and easy to validate and implement. Plug & play automation may eliminate task-specific labor, but all the indirect activities, like sample transfers or incubation and mixing steps, are still manual. Moreover, you can’t just validate an extraction robot by itself – you need the data that come from downstream processes such as quantification and DNA typing. This means that traditional plug and play solutions are not saving as much time or reducing as many variables as you might expect. So, why stop at a single step? Automate more of your process to realize efficiencies in both validation and casework. Today, modularity is about choosing universal robotic solutions that reduce touch points from one step to the next within a given workflow, while increasing reproducibility. Universal robotic platforms expand the contribution that each instrument makes to the overall workflow, decreasing the number of instruments required. They also share common deck accessories, programming language, and even consumable products, enabling flexibility in assay chemistry choice and workflow direction enhancing the lifespan of your capital purchase.
Take a look at your workflow with a fresh set of eyes, and physically map the process. Having this visual helps to eliminate roadblocks and pain points throughout the process, not just at isolated steps. This will inform your purchasing requirements and immediately let you know how the tools you already have are being (under)utilized.
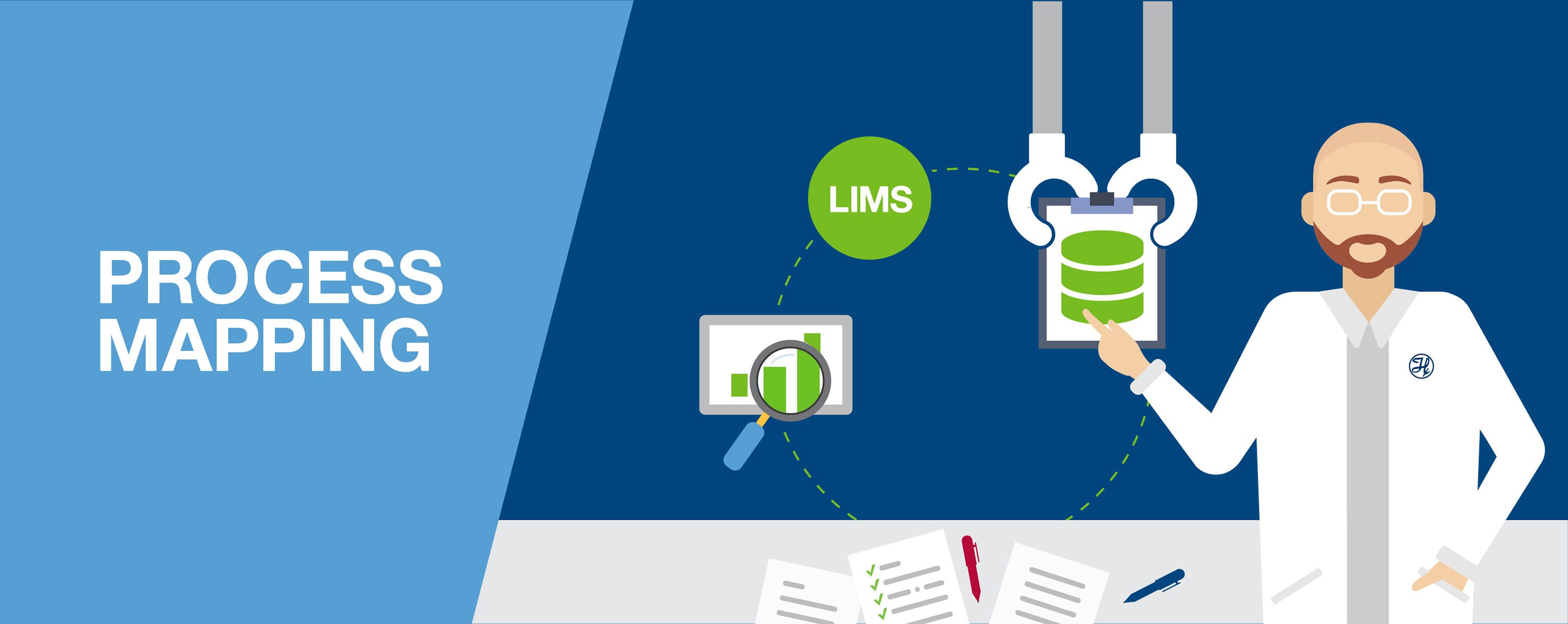
Process Flows to Efficiency
It’s not just workflow or sample flow that matter. Analyst flow through the lab is just as important. Go back to that whole workflow map we talked about and include detail on how people are physically moving through the lab space over time. Include all the details regarding who, what, where, why, and how. You might be surprised at the labor inefficiencies, quality risks, and other bottlenecks that you uncover that can easily be solved by automation.
For example, where can manual handoffs be reduced? This may be as simple as changing labware to a more automation-friendly type. At what points do analysts manually enter data or repetitive information? Worklists are easily, and sometimes automatically, created. How far do analysts transport samples from one step to another? Integrated devices may be less expensive than you think. When are people competing for shared equipment? Scheduling software easily solves this issue. Lastly, consider using everyday laboratory tools like your LIMS, which is commonly underutilized but can provide a beneficial framework for all of your flows.
Understanding this process flow allows you to create smooth, integrated automated workflows that increase throughput, decrease quality issues and unplanned downtime, and reduce turnaround times. On top of that, analysts can spend less time on low value tasks and more time applying their high value expertise where it matters most.
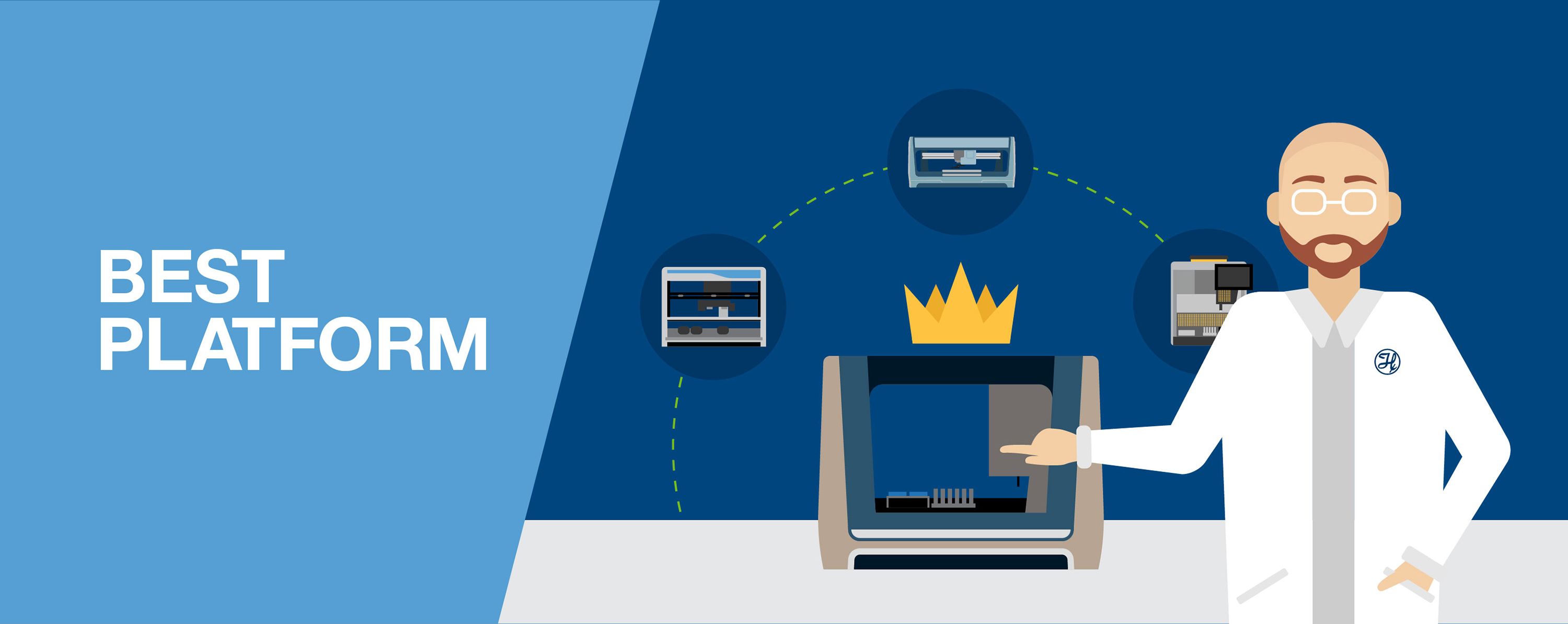
(Deck) Real Estate is King
Sure, throughput is the superstar consideration when selecting a robotic workstation, but the robot’s workable deck area is King! The deck’s size is what enables your workflow to be truly automated. Pipette tips, consumables, reagents, peripheral devices (i.e. heaters, shakers, on-deck thermal cyclers, plate sealers, and more), and samples must all reside on the instrument’s deck.
Need filtered tips for massively parallel sequencing? These don’t stack and, unless you have adequate deck real estate for them, you will be tied to a series of endless labware reloads. Assay mis en place, to borrow a cooking term, reduces manual restocking time and helps the robot to be as efficient as possible when moving labware and samples around the deck. Have a thermal cycling step in the middle of a workflow? An on-deck thermal cycler eliminates multiple manual sample interactions. Once you’ve laid out your process and studied it with colleagues, you can determine how much deck real estate that you need.
Want to really maximize your deck real estate? Opt for a solution with storage for frequently used consumables. Not quite ready yet? That’s okay, too. Modularity in automated liquid handling platforms means that deck layouts can be changed and upgraded as your workflow requirements evolve. Thinking “automation ecosystem” yet?
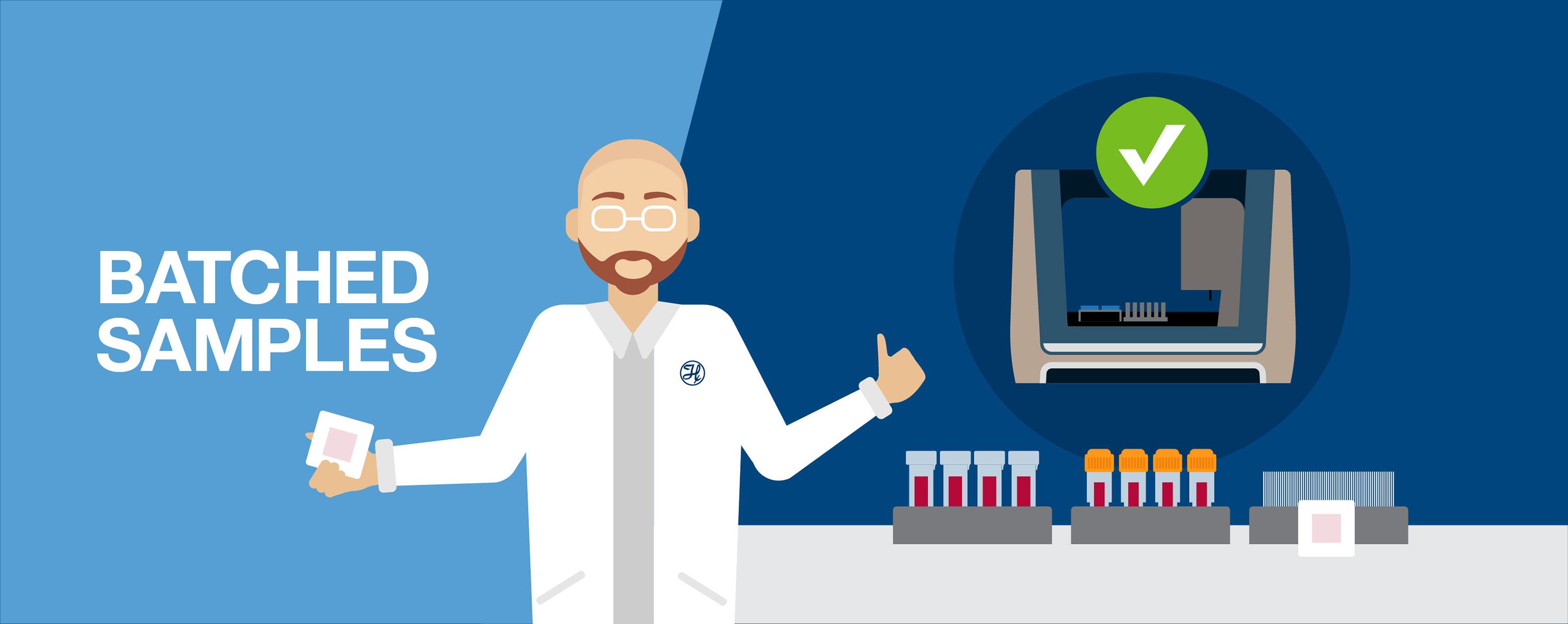
Don’t Let Your Samples Control You
Instead, leverage your automated workflow to reign in the chaos. Streamlined automated workflows already exist for the majority of HID sample types – from simple reference samples to tough evidentiary samples that are environmentally or chemically challenged, degraded, embedded in difficult matrices, of very high or low volume, and more – and separate workflows can be combined on the same instrument to maximize the number of different runs that you can conduct each week.
Your instrumentation is modular and universal, right? So modify your deck and script slightly to alternately work property crimes and sexual assault cases. Saliva on paper got you down? Consider automating samples on specialized matrices within a separate branch of your automated workflow. In this case, add liquid handling to your automated punching device to create a complete sample to answer solution.
Now that you are the master of your samples, look around your deck to see how you can fine tune other workflow details.
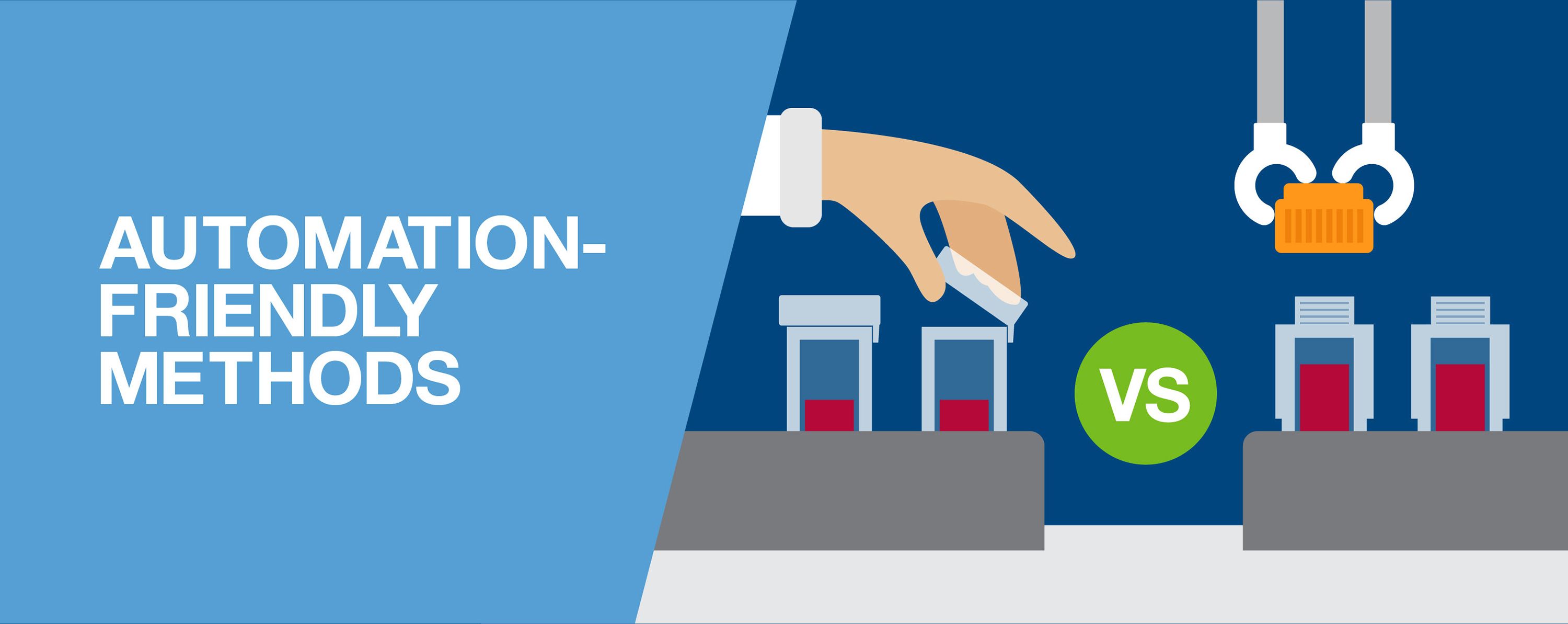
Approach Transformation from Every Detailed Angle
But wait, there’s more! It’s not just the sample. Not just the chemistry. Not even the people. Consider all of the other “stuff” that goes into your process. Consumables and labware vessels can be tricky. Robots can’t reliably manipulate some consumables like unframed FTA paper, microtubes, special tubes such as those with spin baskets, and unskirted PCR plates.
However, most consumable products have automation-friendly alternatives, such as microtubes that can be capped and uncapped in a hands-free manner, completely automatable spin basket tubes that can be expanded and collapsed, and sturdy PCR plates that can be more easily manipulated. All of these products are easily integrated onto universal robotic platforms. On deck peripheral devices like those that we previously mentioned, can perform a variety of actions on automation-friendly consumables, further increasing walk away time
Small changes to the type of consumables, vessels and devices that you use, if needed, can make a big difference in the long run. Not sure what or how to change some of these items? Contact your local automation representative for expert advice.
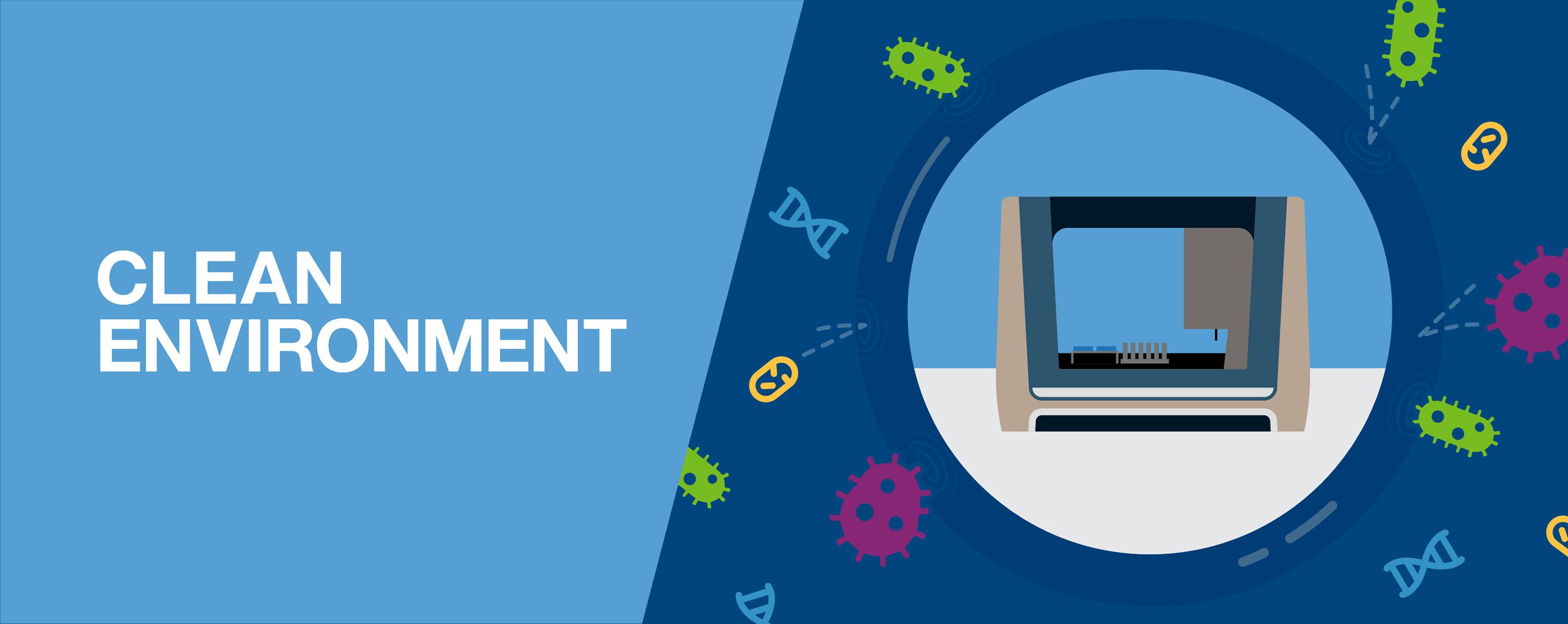
Sterile ≠ Clean
While we are on the topic of consumables, think about this. Why would you specify sterile tips if your reagents aren’t sterile? Sterile means free from microorganisms, but it doesn’t mean free from molecular contaminants like trace nucleic acids, enzymes, and other PCR and DNA typing interferents.
Molecular biology grade assay reagents are tested to be free from molecular contaminants, so it’s only natural to expect this from your pipette tips and consumables, too. Tips from some leading automation manufacturers are made completely robotically without any human intervention. Ask about a manufacturer’s quality standards and lot testing documentation.
If you are concerned about the risk of aerosol contamination, then consider using filter tips. Choose an enclosed liquid handling platform, and go the extra mile in clean air protection by adding features such as integrated HEPA filtration. Lastly, add ultraviolet lamps to your robot to complete your multi-strategy for nucleotide decontamination.
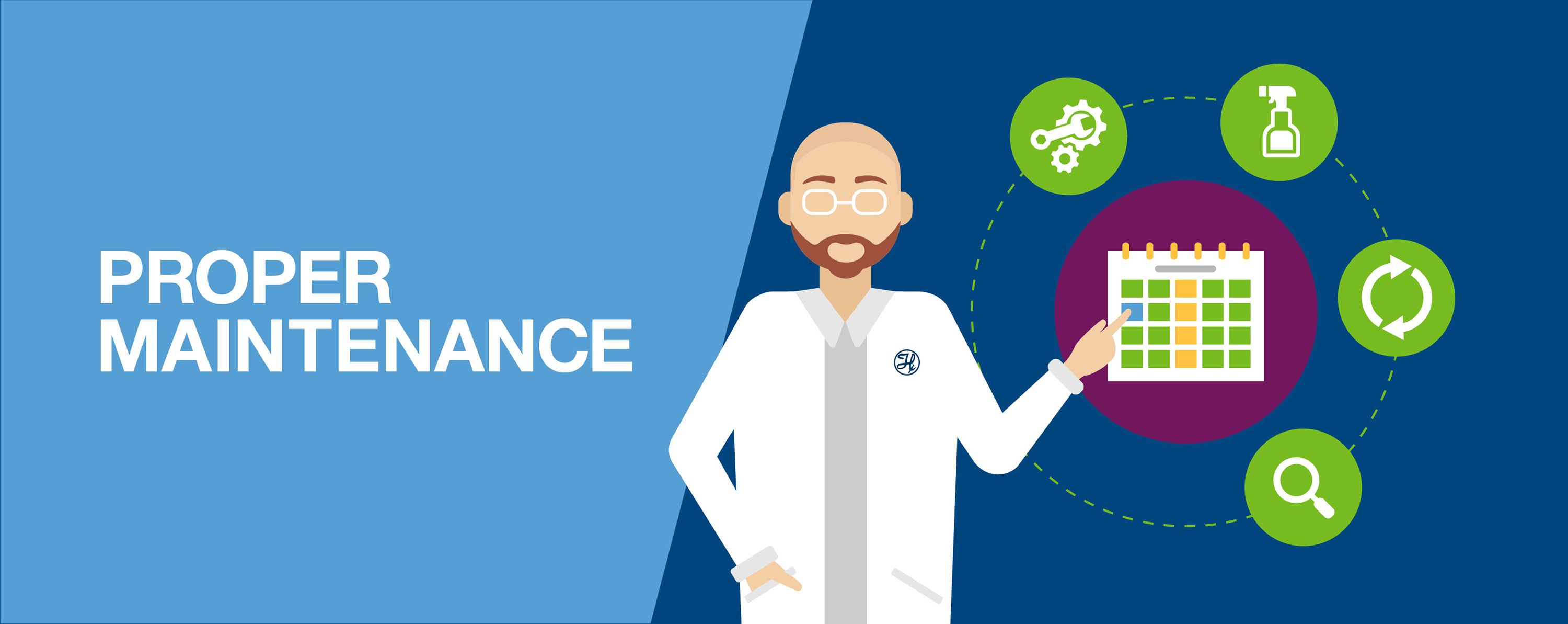
Act Now to Prevent Problems Later
Much like a car engine tune-up, automation maintenance may seem like an afterthought to some naysayers who scoff at the idea of continuous upkeep. But don’t forget overall preventative maintenance measures for your automated workstation. These make sense and keep your workflows running cleanly and smoothly. Your work is a matter of life and death. Literally. Why risk unplanned and disruptive downtime?
Even the seemingly smallest actions, like pre-programmed daily, weekly, and monthly preventative maintenance protocols included in most automated tools help to ensure smooth instrument operation. On top of that, twice yearly automated instrument tune-ups can spot wear-and-tear and correct tiny issues before they grow into major performance deviations that may call into question as much as a full year of data! As an added bonus, integrations such as HEPA filtration, can be rolled into your preventative maintenance plan eliminating the need for a separate benchtop hood and its maintenance plan.
For more information, visit our webpage or email Kevin W.P. Miller, Ph.D.